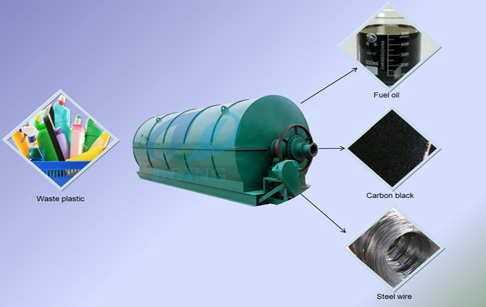
Plastic pyrolysis plant
It is believed that many people know that the principle of pyrolysis of plastics into oil is the process of pyrolysis waste plastics into fuel, carbon black and flammable gases using the principle of high-temperature pyrolysis. Today, this article describes in detail three detailed steps for the pyrolysis of waste plastics into oil. DoingGroup adopts the most advanced and best-performing three-stage condensation in the oil industry to ensure adequate cooling of cracked oil and gas and high oil yield. .
Three steps to pyrolysis plastic to oil
The first step: DoingGroup adopts a vertical condenser, which can generate natural negative pressure. Under natural negative pressure, oil and steam go together to reduce the pressure of the oil outlet, so as to ensure that the oil outlet is not easy to be blocked, compared to the traditional sky tube. , it is easy to block. Can not guarantee the cooling effect of oil and gas.
The second step is to use a horizontal condenser, which is also the condenser with the highest oil yield among the three condensers. The condenser has a large cooling area and can guarantee that more than 90% of oil and gas can be in the condenser at this stage. Cool down. After the first two condensers, only a small part of the oil and gas is not cooled.
The third step: the last vertical condenser is to treat a small amount of oil and gas that has not cooled down in the first and second stages. In order to ensure that this part of the oil and gas is cooled down, oil and gas use a design that moves from the bottom up, which can slow the speed of oil and gas and ensure that the oil and gas are fully cooled.
After these three steps, the cracked oil and gas can be fully cooled. According to different waste plastic materials, the following oil yields are summarized for reference:
Pyrolysis rate of different types of waste plastics:
Raw Materials Project Fuel Oil
Waste plastic PE 85%-95%
PP 80%-90%
PS 80%-90%
ABS 40%
Pure white plastic 60%-70%
Fishing net, safety net 45%-50%
MAMEI 40%
Plastic brand 20%
Pulp 20%-30%
Daily garbage 30%-50%
Pure plastic cable 60%-80%
Pure purchase package 50%
The factors affecting the oil recovery rate mainly depend on the condensing system of the cracking equipment. In addition, the condensing system of the cracking equipment is also related to the degree of dryness and wetness of the recycled plastic waste. In addition, whether the core reactor in the cracking equipment can use the raw material waste The oil and gas in the plastic fully steamed out, which has certain requirements on the quality of the reactor.
DoingGroup's plastic pyrolysis plant
1. The DoingGroup's waste plastic pyrolysis plant not only ensures a higher oil yield from the condensing system, but also uses the Q245R standard boiler plate steel for the reactor, 16mm, curved head, which can withstand high temperature and high pressure.
2. With external insulation system, can play a good thermal insulation effect on the heated reactor.
3. Using a unique three-step welding process, it is not easy to crack and has high safety.
The DoingGroup's waste plastic pyrolysis plant can not only ensure the highest oil output rate in the industry from the condensing unit, but also has enough effort in the design of the reactor. Select DoingGroup, we will also provide you with on-site installation of the equipment, as well as the subsequent operation guidance. Provide you with a professional set of operating instructions to ensure that you can get the maximum oil rate! !